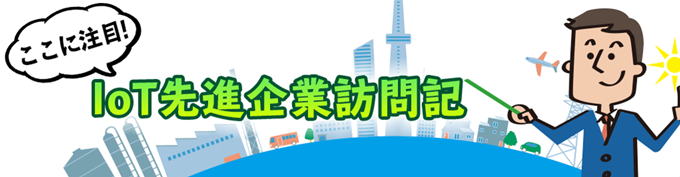
本メルマガは、IoT価値創造推進チームの稲田修一リーダーが取材を行ったIoT導入事例の中から、特に参考となると感じた事業や取り組みを分かりやすくお伝えする見聞記です。
今回は、興味深い事例を投稿いただいた株式会社KMCの佐藤声喜代表取締役社長に、次世代のモノづくりに向けたプロセス改革の話を伺いました。ちなみに、KMCは人間の知恵(Knowledge)を生かしたものづくり(Manufacturing)の仕組みを作る会社(Company)を意味しています。少し長くなりますが、示唆に富んでいるので詳しく紹介いたします。
【ここに注目!IoT先進企業訪問記(5)】
モノづくりの仕組みを変える-KMCのユニークなコンサルティング
昨年は自動車やその部品、金属製品など製造業の不祥事が相次ぎ、Made in Japanの品質評価を著しく損ないました。この問題の根幹は、調達コスト低減を優先した外注化に起因します。例えば、自動車業界では7割が外注。これは経済合理性に基づく行為ですが、外注化を進めれば進めるほど犠牲になるのが品質管理。某エアバッグの会社の事例のように、品質問題は会社の根幹を揺るがす事態を引き起こす危険性を含んでいます。この問題の解決は急務なのです。
1.解決策は「ネットワークケイレツ(系列)」と「ナレッジ(知恵)を融合した情報戦略」
この差し迫った問題の解決策として、そしてモノづくりの競争力を取り戻す戦略として佐藤社長が10年くらい前から提唱し、自ら実践していることが二つあります。一つ目は「ネットワークケイレツ」の構築です。サプライチェーンをIoTでネットワーク化し、多数の製造設備からのデータを一元管理することにより、開発期間短縮、生産性向上、不具合削減を実現しようというものです。データや情報をデジタル化すること、また、これらを社外には出さないという内に閉じた考え方を克服し、企業の枠を超えてサプライチェーン上で活用できるかどうかが鍵となります。
二つ目は「ナレッジを融合した情報戦略」の実現です。技術・ノウハウなどのナレッジをデータベース化し、伝承しようというものです。設計した値、設計理由、判断基準を電子データで記録し、ベテラン技術者によるそれらの修正も合わせて記録することにより、人から人へという形が基本であったノウハウ伝承をデジタルデータ化するのです。この設計情報と現場での生産履歴情報や不具合情報を紐づけすれば、現場の課題を速やかに開発・設計にフィードバックし、ナレッジ進化を促すことが可能になります。ただし、この場合も企業の枠を超えたデータや情報の共有が前提になります。
これらの解決策を具体化するKMCの仕事は現場志向で、極めて現実的です。「データ収集」「業務フロー見直し」「課題解決ノウハウの可視化」という実施の際のボトルネックになる点に着目し、支援しているのです。
2.IoT導入のボトルネックはデータ収集
製造プロセス改革の切り札として、IoT導入、特にIoTプラットフォーム導入に注目が集まっています。話題を呼ぶのは悪いことではありませんが、間違ってはいけないのは、この導入自体で改革が実現するのではないということ。むしろ、改革のスタートにすぎず、その実現に向けた仕組みづくりとその後の継続的な取り組みが不可欠なのです。
IoT導入に際し現場が悩むのは、プラットフォームの活用ではなく、むしろデータ収集の方です。現場には、データを取ることを想定していない古い製造設備が沢山あります。しかも、設備に関する説明資料がない、あったとしても参考にならない場合があります。10~15年後にはすべての設備がデータ対応になり、IoT導入が容易になるのかもしれませんが、現時点でクリアしなければならないのは、既存設備からのデータ収集という高い壁です。
データを取ることが難しいもうひとつの要因は、IoTとモノづくりの両方の知識が必須だからです。モノづくりが分かっていないと、設備や製品の状態を検知するセンサーを選定することが困難です。また、収集データの意味を理解できず、困難にぶつかります。データの粒度や整理法、活用アルゴリズムの開発などにも苦労します。このため、プラットフォームベンダー、PLC注ベンダーはもとより、製造設備メーカですら手を出したがらず、プロセス改革を実現したい企業は現場が自ら考え、工夫することが必要になります。
注:PLCはprogrammable logic controllerの略語。あらかじめ定めた順序に従って、逐次制御を行っていくコントローラーを意味する。
しかし、製造設備からの意味のあるデータ収集に成功すれば、その後のデータ活用は思ったより楽な作業になります。IoTプラットフォームの活用が可能ですし、多くのベンダーがさまざまな提案を出してくれるからです。ある意味、IoT導入が成功するかどうかは、現場におけるデータ収集の成否に90%くらい依存していると言っても過言ではありません。
3.業務フローの見直しはデータや情報の流れがベース
IoT導入によりデータを収集し、分析するだけでは大きな価値を創造できません。それらに基づくプロセス改革が不可欠です。その一番のポイントは外部の目で診断すること。これは、200社以上のプロセス改革を支援した佐藤社長だからこそ言えることです。
例えば、手書きの生産計画表や検査表が存在するプロセスには、無理・無駄が潜んでいます。モノや人が滞留している箇所は、改善の余地があります。しかしながら、さまざまなしがらみや社内力学が働き、人も企業も自分で自分を診断するのは苦手です。だからこそ、外部の目が活きるのです。現場が何となく感じていた問題点や気付かなかった改善点が課題として明確化され、価値創造の第一歩となります。
では、プロセス改革はどう進めたらいいのでしょうか。まずは業務フローを書き出し、工程を把握するとともに、無理・無駄の定量化を行い、自己の姿を定量的に把握します。その上で、目指す姿、具体的目標を設定し、小さな見直しから開始し、その成功をベースに他の見直しに拡げます。
業務フローの見直しにもコツがあります。「データ」や「技術情報」の流れをベースに見直すことがポイントです。紙による情報の受け渡し、人手による検査や品質確認などが多数含まれる生産、計測、検査などのプロセスを「データ」や「技術情報」のやりとりに置き換えます。各プロセスが必要とする「データ」と「技術情報」が見えるようなり、それらがIoT導入により簡単に流通し、かつ、これらを活用して機械が自ら認識、判断できるようにすることで、プロセス改革や業務の効率化が図れます。
さらには、ネットワークケイレツを構築すれば、これを企業や工程の壁を越えて行うことが可能になります。これがIoT導入に際し、本来狙うべき価値なのです。プロセス改革には、最低でも3年という時間が必要です。IoT導入によるプロセス改革のやり方を学習した後、業務フロー見直しを自分達でできるようになるまでの期間です。現場が賢くなると、生産性や品質の向上に向けた次の取り組みが見えるようになり、改革が進展します。長い目で見ると、これが大きな価値創造につながるのです。
4.課題解決ノウハウの可視化でモノづくり競争力復活を
今後、自動化の進展や人工知能の活用により、製造現場の無人化が進むでしょう。しかしながら、非常に高い精度で安定的な品質を追求している製造現場では、日々刻々変わる環境条件に合わせた製造プロセスの調整、不良品発生時の対策が常に発生します。そのような製造プロセスを進化させる仕事をすべて機械に任せることは困難で、人の知恵が必要です。場合によっては、開発や設計にデータをフィードバックし、解決策を探ることも求められます。この判断を行い、問題を解決するのも人の仕事です。つまり人なしでモノづくりを進化させることは、ほぼ不可能なのです。
ここに、我が国がモノづくりで競争力を復活するヒントが潜んでいます。課題解決能力のある技術者を育成することです。モノづくりは、企画→開発→設計→試作→生産設計→製造というプロセスで進みます。問題は、外注により製造と開発・設計の距離が遠くなっていること。これを近づける方法は、設計情報と生産履歴情報や不具合情報を紐づけ、現場の課題を速やかに開発・設計にフィードバックすることです。「ネットワークケイレツ」を構築すれば、これが可能になるのです。
さまざまなナレッジを蓄積したデータベースの構築も重要です。課題解決能力のあるベテラン技術者は忙しく、若手にノウハウ伝承する時間やその内容、相手は限られます。設計や製造、さらに発生した問題に対するベテラン技術者の対応をデータベースに蓄積しておくと、若手技術者はそれを参考に検討することができ、課題解決能力が身に付きます。人工知能の活用は、この「ナレッジを融合した情報戦略」をより有効なものとします。参考となる事例を自動的に抽出してくれるからです。
佐藤社長の仕事内容を見ていると、かなりの部分は現場が自分たちで考え、やるべき仕事のように思えます。実際には、これができないくらい現場が疲弊しているから出番があるのです。今はモノづくりの大変革期です。彼の東奔西走の活躍が実り、我が国のモノづくり競争力が回復することを期待したいと思います。
|
|
|
|
株式会社KMC
|
|
IoT導入事例の募集について