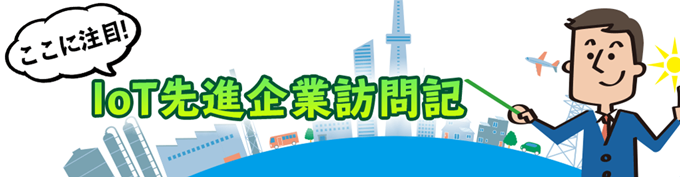
本メルマガは、IoT価値創造推進チームのリーダーである稲田修一が取材を行ったIoT導入事例の中から、特に参考となると感じた事業や取り組みを分かりやすくお伝えする見聞記です。今回から4回にわたり、これまでとは少し趣向を変え、「IoT導入事例」として紹介した事例を分析し、IoT導入のベストプラクティスを考えてみます。
【ここに注目!IoT先進企業訪問記(番外編その1)】
「IoT導入事例」に見る新しい価値の創出法(その1):製品などのIoT化
1.簡単ではない価値創出
今までに70件ほどIoT導入事例を紹介していますが、取材を通じて分かったのは、多くの担当者が価値創出に苦労していることです。データ収集に苦労する、収集したデータを分析可能な形に処理することに苦労する、といったテクニカルな面で苦労するのはもちろんですが、それ以前の初期段階で「どのような価値を創出すべきか」について模索するばかりでなく、IoT導入後もこの実現に向けて試行錯誤を続けるケースが多いのです。創出する価値はアイデア次第で多様ですが、そこには共通する成功ノウハウがあるように思います。第1回目の今回は、製品などのIoT化による価値創出のノウハウに迫ってみたいと思います。
2.製品などのIoT化による価値創出の基本パターン
製品やサービス、システムなどをIoT化すると、状態を把握し、それを改善することで価値創出につなげることができるようになります。産業優位性を築く競争戦略の研究で大きな功績をあげているハーバード大学のマイケル・ポーター教授は、製品などをネットワークに接続しデータ収集・活用することで、最初は「モニタリング」、次に「制御」、三番目にモニタリングと制御をもとにした「最適化」、そして最後はそれをさらに推し進めることで実現する「自動化」という価値が創出されると述べています(下図参照)。
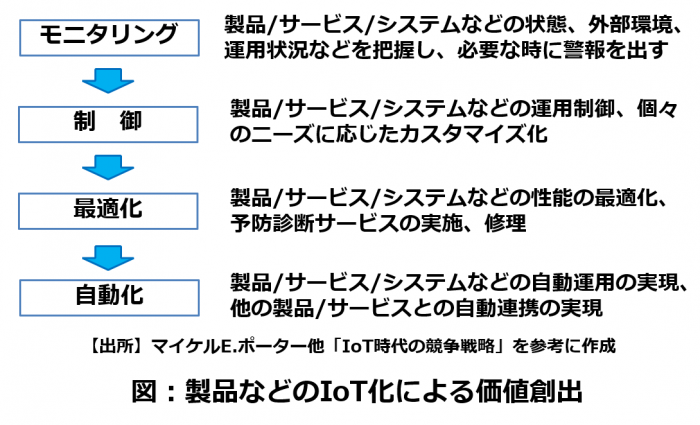
ネットワークに接続されたOA機器をリモートモニタリングして稼働状況を把握し、保守運用の効率化を実現しているリコーの事例(https://smartiot-forum.jp/iot-val-team/iot-case/iot-case-ricoh)、グループ全体で足並みを揃えた生産改革を進めるために、世界各地の工場で収集した生産機械の稼働データの活用を進めているYKKの事例(https://smartiot-forum.jp/iot-val-team/iot-case/case-ykk)はこの典型例です。
3.創出される価値と適用領域
IoT化によって創出される価値は、プロセス管理の最適化、生産効率の改善、故障や異常の兆候の検出、保守の最適化、作業の自動化、需要量の予測に応じた生産量の調整、オフィス環境や居住環境の快適化、サプライチェーン全体の省人化・自動化・最適化など、さまざまです。
IoT化が特に有用な領域はいくつかあります。その典型例は「ものづくり」「もの売り」「保守・運用」など、現場が重要な役割を果たしている領域です。ここでいう「ものづくり」の中には、製造業だけでなく、農業、林業や養殖漁業なども含まれます。これからの時代は画一的な商品やサービスの提供ではなく、個別ニーズに沿った商品やサービスをきめ細かく提供することが求められます。これをスピーディ、かつ柔軟に提供する仕組みを実現するのがIoT化による「モニタリング」⇒「制御」⇒「最適化」⇒「自動化」という考え方なのです。
4.事例から考えるIoT化のベストプラクティス
4.1 経営者のリーダーシップ
生産プロセス全体の改革をIoT導入で進める、IoT導入で収集したデータをコトづくりやサービス提供に結び付け新たな収益源に育てるなど、会社全体の将来に大きな影響を与えるIoT導入に関しては、経営者の判断で導入検討が始まったケースが大半です。事業部の壁を越える調整が必要となる可能性が高く、かつ、新しい仕組みの導入に前向きではない社員や顧客が多い日本の組織の現状を考えると、経営者のリーダーシップという強い推進力の存在は不可欠です。
4.2 明確な目標設定それを実現する仕組みの構築
価値創出の成功に向けた動きが顕在化している事例を見ていると、興味深い共通点に気がつきます。それは顧客や経営者から明確な目標が示され、担当がこれを実現する仕組みを構築していることです。具体例を紹介しましょう。
4.2.1 データから課題を読み取り改善を重ねる「人」を活用したKMC
コニカミノルタの統合サプライチェーンマネジメント・システムを構築したKMC注の場合(https://smartiot-forum.jp/iot-val-team/iot-case/case-kmc04)は、顧客のコニカミノルタから「人・場所・国・変動に依存しないものづくり」「生産のQCD(品質・コスト・納期)改善」「(需要に応じた)フレキシビリテイ生産の実現」という目標を示されています。
コニカミノルタが示した目標の達成には、既存システムと連携した全体ソリューションを考えることが不可欠です。このため、KMCは製造情報、製造ログデータ、不具合状態データなどデータをベースにサプライチェーン全体の現状と課題を分析し、生産性向上や不良の予知・予防を可能とするIoT化の道筋をまず考えています。そしてこの実現に向け、IoT化が難しい古い生産機械を含めた全体のIoT化を行っています。
また、QCDの改善には、現場が納得してIoTを使いこなすことが不可欠なので、現場作業時の操作の容易性などにもこだわっています。示された目標を達成するには、IoT導入後に人がデータから課題を読み取って不断な改善を続けることが鍵となるので、その実行を促進する仕組みを考え、構築したのです。
注:KMC(本社:川崎市高津区)は、IoT/M2Mを活用した生産システム革新のためのコンサルティング、研究開発、ソフト開発を行っている。KMCは、人間の知恵(Knowledge)を生かしたものづくり(Manufacturing)の仕組みを作る会社(Company)を意味する。
4.2.2 PDCAサイクルを回した中村留精密工業
一方、石川県を拠点とする中堅工作機械メーカーである中村留精密工業の場合(https://smartiot-forum.jp/iot-val-team/iot-case/case-nakamura-tome)は、社長から「30%以上の生産性改善」という目標が示されています。
同社の担当は、この達成には従来の枠を超えた会社全体の効率改善が必要だと考えました。このため、①社内の活動に伴うデータの収集と可視化、②分析による課題の発見、③改善対策の実施、④新たな課題の発見に向けたデータ収集項目の見直し、というPDCAサイクルを回す仕組みを全社展開し、改善を積み上げています。同社も、人がデータから課題を読み取り、継続的に改善することが鍵だと考えたのです。
4.2.3 仕組みづくりを誘発する明確な目標設定が重要な理由
ポーター教授が述べているように、IoT導入で創出される価値は「モニタリング」⇒「制御」⇒「最適化」⇒「自動化」という段階を経て進化する一面を持っています。そして、これをより高度なものに進化させるには、モニタリングや制御対象の拡大、その精度の向上、最適化範囲の拡大、あるいは自動化に向けたプロセス変更などの取り組みを絶え間なく繰り返すことが重要になります。これは「改善の積み重ね」という日本企業が得意な領域です。IoTは単なるツールであり、この導入が直ちに大きな価値創出に結び付くのではありません。これには人が関わる改善の積み重ねが不可欠であり、だからこそ高い目標を示すことで仕組みづくりが不可欠だと認識させることが有用なのです。
4.3 トップ直属のIoT導入チームの設置
いくつかの企業は全社的なIoT導入を促進するため、IoT導入チームを設置し、パイロットプロジェクトを始めとする全社的なプロジェクトに取り組むと同時に、組織内のさまざまなプロジェクトを支援しています。ICTユーザ企業の多くでは、情報通信技術に詳しい人材が限られる場合が多いことから、このようなチームの設置は数少ない人材を有効に活用するために必須です。
また、このチームをトップ直属にすることも重要です。IoTシステムは、多くの事業部や現場をまたがるシステムになります。また、同時に経営判断に直結するシステムです。このため、トップが旗振りをしないと全社的なコンセンサスを得るのに時間がかかりますし、協力しない部署が出てプロジェクトが行き詰まる可能性も高くなります。4.2で述べたように、今までとは違う新しい仕組みの構築が必要で、かつ、成果が明確な形で感じられるようになるまでに相当数のエフォートが必要ですので、経営層のリーダーシップと理解なしにはその推進が難しいのです。
4.4 早期に成果が見えるパイロットプロジェクトの選定・実施
成功確率が高く、例えば6~12ヵ月という比較的短期間で社内が納得する成果を示すことのできるパイロットプロジェクトを選定し、社内にIoT導入の機運を高めることも重要です。これを上手に実施したのは、スイッチング電源とノイズフィルタの専業のコーセル(本社:富山県富山市)(https://smartiot-forum.jp/iot-val-team/iot-case/case-cosel)です。同社は、生産システム全体の課題を分析し、生産システム革新の将来像を描き、その中でIoT導入による解決策を考えていますが、短期間で成果が見える小さな成功で現場の納得を得ながら、同時に、時間はかかるが大きな成果につながる開発案件も合わせて実施し、全社的なスマートファクトリー化を進めています。
IoT導入で現場が直ちに改善される訳ではありません。現場を改善するには、データを読んで課題を把握すると同時に、それを解決する「アイデア出し」が不可欠です。これが得意なのは現場が分かっている人達です。彼らがIoT導入の意義を理解し、課題解決アイデアを提案するなど、積極的に協力することが成功の鍵となるのです。このため、IoT推進部隊が現場と建設的な対話ができる関係を構築することに加え、現場がIoT導入の重要性とそれによる変化についての理解を深め、やる気になることが重要なのです。人のマインドを変えるために小さな成功が必要なのです。
4.5 IoT化に必要な能力を確保・育成するための人材戦略
IoT導入では今までとは異なる能力が必要になります。それは「データから課題を読み取る能力」「改善に必要なソフトウェアをスピーディに開発する能力」です。これらの能力を有する人材は、ICT企業を除く多くの企業では極めて少人数なので、必要な人材を揃える工夫が必要になります。
これには、大きく分けて二つのやり方があります。一つは知見を有するICT企業の人材を活用するやり方、それから自社で人材を育成するやり方です。自社で人材を育成する場合は、組織トップ直属のIoT導入チームに数少ない人材を集め、パイロットプロジェクトなどを通じたオンザジョブトレーニングで人材育成を行うことが現実的です。ICT企業の人材を活用する場合も、社内人材の育成・確保は不可欠です。
4.5.1 オープンソースの活用
中村留精密工業は、PDCAサイクルを回すために必要な「稼働状況や進捗状況の可視化」「集計結果の分析」「スケジュールや工数管理など工程最適化」を実現するソフトウェアをオープンソース・ソフトウェア(OSS)を活用し、自社開発しています。データから課題を見つけ改善するには、収集データやソフトウェアを柔軟に変更することが不可欠だと考え、そうしたのです。この決断は成功でした。プロジェクト開始当初はOSSを使いこなすノウハウがなく、ネット情報を頼りにノウハウ蓄積を行うなど苦労したそうですが、やっているうちにOSS活用に慣れ、少人数でスピーディな開発が可能になりました。
中堅以下の規模の企業のIoT化には、コスト面の制約と機動的なプロセス改善のために自前でソフトウェア開発する能力を身に付けることが不可欠です。同社の場合、OSSの活用に加え、辛抱強く社内のソフトウェア技術者育成に取り組んだことが、この実現につながっています。
5.まとめ
本稿で述べたIoT導入のベストプラクティスをまとめると、次の5点となります。
① 経営者のリーダーシップ
② 明確な目標設定とそれを実現する仕組みの構築
③ 全社的なプロジェクトに取り組むと同時に組織内のさまざまな部門の
プロジェクトを支援するトップ直属のIoT導入チームの設置
④ 早期に成果が見えるパイロットプロジェクトの選定・実施
⑤ IoT化に必要な能力を確保・育成するための人材戦略
このまとめは、IoTだけでなくさまざまな新規技術や手法を導入する際に活用できるノウハウだと思います。
スマートIoT推進フォーラムでは、 会員の皆様からIoT導入事例を募集しております
詳細は以下を御覧ください。
IoT導入事例の募集について
IoT導入事例の募集について