IoT導入のきっかけ、背景
YKKグループは、ファスナーやスナップ&ボタンなどのファスニング事業と窓やドアなどのAP事業(建材事業)を中核としており、その両事業の一貫生産を支える工機技術本部を加えた、3者による事業経営と世界6極による地域経営を基本としています。本記事では、ファスニング事業におけるIoT活用の取り組みについて紹介します。ファスナーは衣料品の他にも多くの用途で使われており、中には何回も開け閉めする使用頻度の高い用途もあります。高い品質を実現するために、マーケティング・商品企画から販売・サービスに至るバリューチェーンにおいて、材料開発や加工技術、設備・ラインの開発、機械や部品・金型製造に至るまでを自社で一貫して行っています。現在では必ずしも内製化に拘らず、競争力を第一に考えて展開していますが、この一貫生産思想は経営の根幹であり、今後も強化・継続していきます。
YKKは市場(お客様)の近くで工場を展開し、お客様の要望にきめ細かくタイムリーに対応し続けることを事業戦略としています。そのため、お客様であるアパレルメーカーや縫製工場がある国と地域に工場を展開し続け、現在では73の国と地域で事業活動を行っています。海外との連絡手段が電話やFAXの時代から海外展開を行ってきた経緯から、現地での自律した経営体制を基本としてきました。何か問題が発生した際は現地で解決し、生産を止めない体制を構築してきました。
一方で、世界的な縫製地の変化に伴いYKKの工場立地も変化し、新興国である南アジアなどへの生産シフトが加速しています。これに伴い、生産性に影響を与える、操業経験の蓄積が工場毎に異なるなど、工場の多様化が進んでいます。
これまで世界の各工場で、内製設備を勘と経験で使用してきた部分もあり、分析や改良・改善を都度行ってきたものの、統一したデータ管理に基づく視点が欠けていました。そこで、YKKのビジネスモデルである一貫生産思想を進化させる為に、設備総合効率に基づく設備関連データを統合して活用する計画を進めています。ファスナーの生産工場は現在、世界で約50工場あり、そこには約3万台の生産設備が稼働しています。その内の約1万台・生産量の80%を占める機械から情報を取集することで、生産部門のコストダウンやリードタイム短縮に繋げます。また設備開発部門でも、設備の改善・改良・進化に活用し、設備・部品製造部門においては、保守部品の安定供給に繋げていきます。
これまでも海外の主要工場の一部で設備総合効率を指標としてはいましたが、設備の稼働状態をデータで正確に表すことを目的に、全工場が同じ言葉・数字を共有し本質的な改善に繋げることを方針に定め、2014年から取り組みを開始、2015年にはデータ収集の仕組みづくりと合わせて、各工場への展開を進めてきました。
従来の勘と経験による設備運用・保全から、原理原則に基づくデータの活用によって、コストダウン、設備開発、予防保全の改良・改善・進化に繋げていく予定です。
IoT事例の概要
今回行った取り組みの概要と成果を以下に示します。
海外工場の設備状況データの見える化およびデータ分析
従来からチョコ停がいつ何回というレベルのデータは取得していたが、立地条件の差異から生じる、工場固有の生産ロスの発生原因までは分からなかった。グループ全体で足並みを揃えて生産改革を進めるためには、この工場固有の事象を明確にする必要がありました。
そこで、図-1に示すように生産ロスの発生要因を8つに細分化し、それぞれの発生時間を計測。必要なデータは、生産設備からPLC経由で収集し、このデータから「設備総合効率」を求め、改善の進捗を測るグループ共通の指標としました。一貫生産思想に基づき設備を自社開発しているため、このようなデータ収集が可能でした。
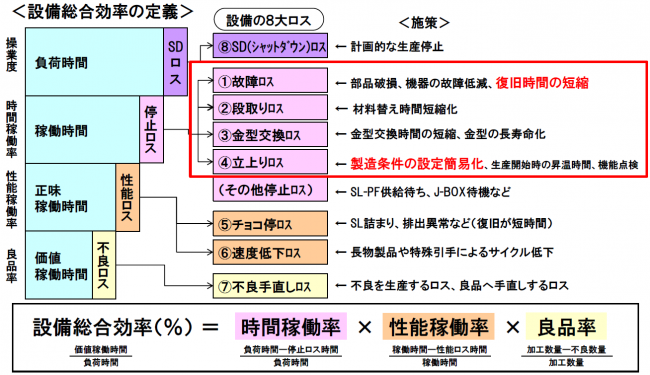
収集したデータを各工場で分析し、同じデータを見ながら議論することによって、各工場がより自律的に改善点を発見できるようになりました。各工場固有の課題を発見しながら、グループ共通の目標達成に向けて改善活動を行う仕組みを進めています。
また、本データを全世界の工場に公開することによって、工場間の競争意識が芽生え、施策の推進を加速できています。
ベテラン保全工のノウハウの数値化
熟練保全工は設備の作動音で好不調を聞き分けることができます。そのため、設備のモデル機種についてマシンパーツ交換前と交換後の試運転で収集した動作音や振動を数値化し、聴音等による不具合箇所の特定ができるようにしました。データの分析には機械学習を使用しています。
データに基づくマシンパーツ寿命基準の設定
この取り組みでは、従来の「勘と経験」による設備保全から、「データと原理原則」に基づく保全を進めています。例えば生産で欠かすことができない金型は、設備の稼働に伴う摩耗が発生するため、定期的に交換が必要です。従来からマシンパーツ交換の基準は定めていましたが、最終的な交換の判断は、保全工の経験則に依存する部分がありました。工場毎の気候や生産条件によって摩耗の進行が異なり、ここに保全工の経験則が生かされていました。
そこで、「金属の摩耗の原理原則と設備稼働のデータ」から損傷予測式を定め、交換時期を予測するようにしました。これによって、マシンパーツストックの余剰によるコスト増を抑制することができました。
取り組みの全体像
今回の取り組みの全体像を図-2に示します。
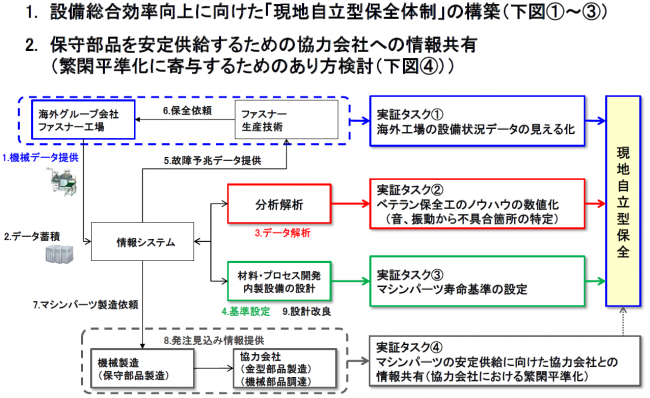
この取り組みによって、世界各国の工場で収集した稼働データによる設備の改善 → 改善結果を展開することによるコストダウン・リードタイムの短縮 → さらなる改善要望の発見という、改善のループの形成を進めています(図-3を参照)
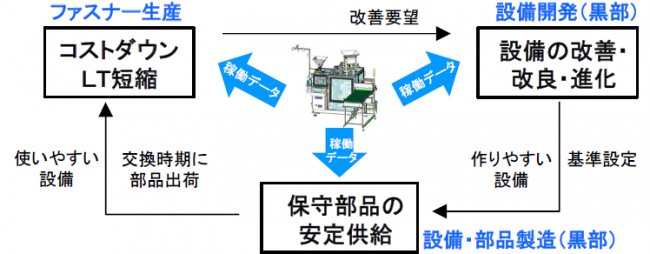
事業化への道のり
苦労した点、解決したハードル、導入にかかった期間
世界中の工場にこの施策を浸透させるのに時間を要しました。また、設備総合効率は工場の成績表ともいえるため、当初は悪い情報の開示に対する抵抗もありました。こうした中、トップダウンで情報公開を推進した結果、最終的には工場の理解も得られ、かつベストプラクティスとして他の工場のデータを有効に活用できるようになりました。
導入展開では用語の定義を明確化し、数値の持つ意味を周知するとともに、 各社の設備総合効率の見える化(公表)を実施。競争原理が働き、各社が自発的に目標を設定してコストダウンを推進するようになり、取り組みが加速していきました。今では、各社が前年比改善を目指し、主体的に製造現場の 改善・改良を進めています。
技術開発を必要とした事項または利活用・参考としたもの
BI(Business Intelligence)ツールは社外製品をカスタマイズした。可視化や分析のためのソフトウェアは社内で開発している。
今後の展開
現在抱えている課題、将来的に想定する課題
今後は、各システム運用の評価・改善を行いながら、海外各社からのデータ収集の拡大を進める予定です。
尚、海外からのデータ収集やフィードバックにおいて、データ容量増加に伴い、実用に耐えるネットワークインフラの構築を課題としています。又、情報共有におけるセキュリティ対策も含め、IT関連の課題と認識しています。
強化していきたいポイント、将来に向けて考えられる行動
海外工場の設備状況データの見える化に関しては、対象工場・機種の拡大などを進めていきたい。ベテラン保全工のノウハウの数値化に関しては、データに基づく設備の改善・改良、進化につなげていきたい。マシンパーツの寿命に関しては基準の精度向上、短寿命部品の長寿命化を実現したい。繁閑平準化のために行った協力会社との情報共有については、これをさらに進めて、協力会社との取引の電子化(例えば、発注後の製造進捗の共有)を図りたい。
生産現場と設備開発者の更なる意識改革、今後の実証活動を通じた本質的課題の抽出を進めます。