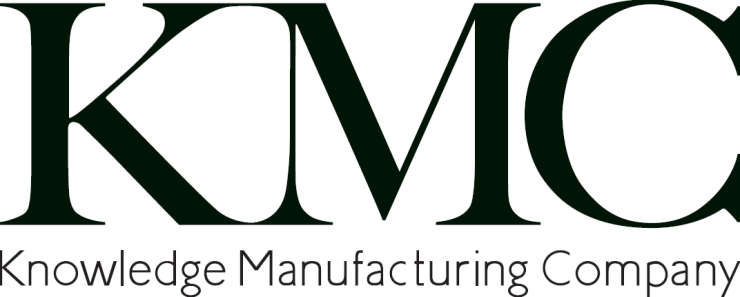
株式会社KMC
- 製造(その他)(部品製造を実施している製造業)
- コスト削減
- 事業・業務の見える化
- 事業・業務プロセスの改善
- 売上向上
事業継続性
- 故障や異常の予兆の検知、予防
- 故障や異常への迅速な措置
その他
- 作業の容易性向上、人員不足解消、不良品削減、紙記入排除
【活用対象】
- 企業顧客
IoT導入のきっかけ、背景
株式会社KMC (以下、当社)は、「製造現場の改革無くして成長はない」という当社代表・佐藤の持論のもと、製造現場のDX化を支援する企業として2010年に設立された。
当社の主軸は、次の4つのカテゴリの事業である。(図1)
・生産:設備 IoT及びM2M
・生産技術:金型IoT
・設計:開発IoT
・センシング:無線センサ等
特に、ここ3年はセンサの開発に注力し、独自の無線センサを多数市場投入している。製造現場を見渡すと工場の設備の98%は古い設備であり、最新鋭のIoT対応の設備が入っているところは非常に少ない。古い設備をDX設備に転換するには、簡単に設置できる無線センサが必要なのである。
なお、当社は、2018年度には経産省より【はばたく中小企業300社】の中の一社として表彰されているhttps://www.chusho.meti.go.jp/keiei/sapoin/monozukuri300sha/zenbun/2018habataku.pdf
図1:KMC のDXソリューション(出所:KMC 提供資料)
IoT事例の概要
サービス名等、関連URL、主な導入企業名
・サービス名:製造DXソリューション
・関連URL:電承FCATRY https://www.densho-factory.com
・導入先:部品製造を実施している製造業
・導入事例:https://www.densho-factory.com/case/
サービスやビジネスモデルの概要
最近の世の中のニーズに照らし合わせると、まずはデータを「取る・見る・分析・活かす」というデジタルカイゼンのPDCAサイクルを回すことが製造業にとっては非常に重要である。(図2)
単にIoTシステム、M2Mシステムを入れただけでは、だいたい1年もすると陳腐化して使われなくなる。これを防ぐには、現場からデータをきちんと取得し、それを見て、分析して、それがどう役に立つのか、どう活かせばいいのかを考え、デジタルカイゼンを実行していくことが必要である。当社はユーザーからの依頼に応じデジタルカイゼン支援を行っているが、取ったデータをどう活かすかが一番の課題である。
図2:デジタルカイゼンPDCA(出所:KMC 提供資料)
内容詳細
顧客からの依頼、問い合わせには大きく2つがある。
・不良を出さない
・生産(機械)を止めない
図3が当社が提供するDXソリューションの全体マップである。左下は設備情報の収集を表す。生産設備は時としてチョコ停注1と言われるトラブルを起こすが、これを削減、抑止するためにM2M(Mashine to Mashine)ソリューションで設備の状態監視を行っている。
図3の真ん中では、「人・機械・材料・方法」のいわゆる4M情報の収集を表している。メインとなる設備(プレス機、成形機)をはじめ、材料、作業者、方法(工程)、さらには金型を加えた5Mの情報をQRコードにより取得し、情報管理を行っている。作業者によるレベル差低減のため、人の情報を取得することは非常に重要だ。そして図3の右側下では現場情報の収集を表している。検査情報、在庫管理、作業日報や機械日報といった各種情報を、タブレット端末を使用してデジタルに現場データを収集することで工程のトレーサビリティが実現できる。当社ではこれらをまとめて「製造IoT」としている。その上位には「開発IoT」が存在し、現場から得られた様々な情報を開発側にフィードバックすることを可能としている。
注1:ラインなどの製造設備がわずかな時間だけ停止してしまうトラブル
図3:製造DXソリューション構成(出所:KMC提供資料)
さらに、当社は各種センサを使用して製造ラインのさまざまなセンシングを展開している。図4は成形現場での事例である。成形機の周辺には、金型・温調器・乾燥機など様々な周辺機器があるが、これらすべてのデータを取らなければ不良の原因は検出できない。
しかし、残念ながら周辺機器を含めこれら設備を提供するメーカは複数にまたがるため、すべてを取りまとめる企業はなく、配線業者もいない。そのため、当社はこれをワンストップで引き受け、成形機だけでなく全ての設備・機器の状態を把握・監視できるようにしている。当社が手掛けたこれまでシステムは、国内外含めて800台程度稼働している。
図4:成形機センシング事例(出所:KMC提供資料)
取り扱うデータの概要とその活用法
当社は、製造現場の様々なデータ収集と活用支援を行っている。ユーザー側が実現したいと考えるDXの目的に照らし合わせて収集するデータを決めるが、データは現場が困っている不良等の原因によっても変化する。例えば、上記の成形現場の事例では、設備から次のデータを収集している。
・温調器の温度管理データ
温調器の水温データ
・成形品に関するデータ
金型の温度データ
材料を押し出すスクリューの回転データ
DX実現への道のり
DX実現にあたり苦労した点、解決したハードル、導入にかかった期間
日本の製造現場は、変化を嫌う。今まで実施してきた作業、そして今実施している作業を変えることに異常な抵抗を示す。製造現場におけるDX化とは、これまでの経験と勘に基づく生産から、デジタルデータによる管理のもとでの生産へと移行することである。製造現場を改革するには、ひとつひとつ丁寧に説明、説得し、DXの効果を実感してもらうことが必要だ。DX化を受け入れてもらうまでに時間がかかるだけでなく、ひとつでも間違えると改革がとまってしまう。
当社では、現場の人に使ってもらえるシステムにすることが解決策であると考え、ソリューションの提供だけでなく、コンサルティングにより使い勝手の面におけるサポートも実施している。サポートが手厚くなければ製造現場、特に中小企業には受け入れられない。
現場が良くなると、必然的にQCD注2は上がっていく。しかしながら、経営トップと製造現場とのギャップは非常に大きい。経営トップが求める利益、生産性向上につなげていくには、やはり時間がかかる。経営トップが求める成果を実現するまでには、DX化に着手してから3年くらいの時間は要するだろう。
注2:品質(Quality)・コスト(Cost)・納期(Delivery)の頭文字をとった用語で、製造業には欠かすことのできない3要素。
技術開発を必要とした事項または利活用・参考としたもの
当社では、特に古い設備からのデータ収集を実現するために、無線センサタグ(STETHOSCOPE)を開発した。設備や金型の健康状態について、後付けのセンサで監視できるようにするためである。無線方式のため電源やPLC注3の準備や配線工事が不要で、既存の古い設備にも簡単に設置できる。設置当日よりデータを収集する事が可能だ。
当社の無線センサでは、以下のセンシングに幅広く利用している。
・温度センシング
・回転センシング
・電流センシング
・振動センシング
・圧力センシング
・稼働センシング
注3:Programmable Logic Controller、プログラマブルロジックコントローラのこと、主に製造業の装置などの制御に使用されるコントローラである。
図5:無線センシング(STETHOSCOPE)(出所:KMC HP掲載)
DXの今後の展開
現在抱えている課題、将来的に想定する課題
当社がDX化の支援を行って痛感したことは、相手先に改善を引っ張っていくキーマン、カウンタパーソンが最低でも1名はいないとDXは実現できないということである。
また、改善にはユーザー側にチームを作ってもらうことも必要だ。当社以外のチームメンバーが自分たちで改善のPDCA注4サイクルを回せるように、データから気づきを得ることができる人材が必要となる。このため人材育成は不可欠であり、DXソリューションを導入後、チーム内で勉強していくことが必要となる。
注4:Plan(計画)、Do(実行)、Check(評価)、Action(改善)の頭文字を取ったもの
強化していきたいポイント、将来に向けて考えられる行動
製造現場で金型不良や製品不良を起こしている原因は、根本となる金型の設計に問題があるというケースは多い。しかしながら、その事実を知らない設計者もまた多い。真のカイゼンを実現するには、現場のデータを金型設計、製品設計にフィードバックして、最初から不良が起きない設計をすることが重要である。