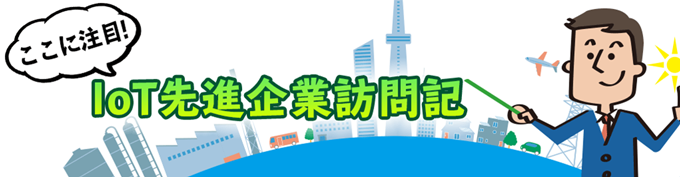
本メルマガは、IoT価値創造推進チームのリーダーである稲田修一が取材を行ったIoT導入事例の中から、特に参考となると感じた事業や取り組みを分かりやすくお伝えする見聞記です。
今回は、株式会社KMC(本社:神奈川県川崎市)の取り組みを紹介します。
【ここに注目!IoT先進企業訪問記 第69回】
製造現場の改革なくして成長はないーKMCのモノづくりDXの実践
1. はじめに
株式会社KMC(本社:神奈川県川崎市高津区)の佐藤声喜代表取締役社長は、さまざまな現場で工程改革に成功されたその道のプロです。同社は、これからの製造改革のキーワードになるのは「データ」であり、IoT/M2M で新世代のものづくりを支援しようということで、2010年に設立されました。ちなみに、KMCは人間の知恵(Knowledge)を生かしたものづくり(Manufacturing)の仕組みを作る会社(Company)を意味しています。
2. センサから始めないとモノづくりDXは進まない
佐藤社長は2008年頃から製造業の競争力を取り戻す戦略として「ネットワークケイレツ(系列)」と「ナレッジ(知恵)を融合した情報戦略」を提唱し、自ら実践されていました。ドイツ発のインダストリー4.0と同じ概念です。そのツールとして金型IoTや設備IoT、開発IoTという商品群を提供していたのですが、最近、センサ類も提供しています。(図1参照 赤線で囲んだ部分がこの3年間で商品一覧に追加されたセンサ類)
図1:KMCの商品一覧
(出所:KMCホームページ(2022年7月24日))
https://www.densho-factory.com/
センサ類の提供を開始した理由は明快です。製造工程の状態を的確にモニタリングするために必要なセンサ装置に適切なものが少ないからです。人口減の日本の製造現場では、ロボットだけでなく、製造や設備の情報を自動的に収集するセンサ装置が必要です。このため、モノづくりDXのスタートラインは、末端のセンサ装置でデータをとることだと判断し、ここ3年ほどその開発・提供に力をいれています。
機械設備に貼り付けるだけで温度、振動、圧力、回転数、電流などを簡単に計測し、データ収集することを可能とする無線センサタグ、不良品の発生や金型の破損を防ぐために金型の表面温度をきめ細かく監視する「金型表面温度センサ(サーモモニタリン)」などのセンサ装置を開発したところ、価格が手ごろだったこともあり好評でした。現在、同社はリアルデータを収集し「過去トラ(過去に起こったトラブル)」ではなく、「現トラ(現在起こっているトラブル)」で品質を改善しよう、という掛け声でセンサ装置のビジネスを推進しています。
3. モノづくりDXが進まない原因は古い機械の存在
日本の製造業、特に中小企業ではモノづくりDXが進展していません。進んでいると言われている企業でも、その実態は機械設備にセンサ装置を取り付けて何とかデータを活用している段階です。データをモノづくりDXに結びつけている、とはとても言えない状態です。この遅れの大きな原因の一つは古い機械設備の存在です。
我が国の製造現場にある機械設備の大半は、15年以上経ったものです。新しい機械設備にはデータを収集する仕組みが備わっていますが、古いものにはそのような仕組みがなく、後付けでデータ収集する装置を取り付ける必要があります。また、最新の機械設備であっても、実際の製造現場では周辺装置と組み合わせて使うため、製造工程を見える化するにはこれらの周辺装置を含めたデータ収集が必要となります。しかし、設備と周辺装置では製造メーカが異なるケースが多く、これらの設備等をまとめて面倒を見てくれる製造メーカはないそうです。
モノづくりDXを推進する前にデータ収集という高い壁があり、この壁を超えるためにセンサ装置から手掛ける必要があったのです。
4. 変化を嫌う現場もモノづくりDXの障害要因
多くの企業でモノづくりDXが進んでいないもう一つの原因は、異常なほど変化を嫌う現場の存在です。100年に一度と言われる変革期に突入し、生存をかけたグローバルな戦いの真っただ中にいるのに、現場ではその時代の変化が見えていないのです。
DXを推進しようとすると「導入効果が見えない」「やる人がいない」「費用が高い」「学生じゃないからタブレットは使えない」など、ネガティブな意見が出ることが通例です。センサ装置を取り付けた後も、「成形機の製造データを取ってもどう扱えばよいのか」「閾値はどうやって決めるのか」など、データの取り扱いに関する基本的なところから説明が必要です。このため、DX技術に関するコンサルティングや導入支援が欠かせません。
5. 現場をやる気にさせDXへと駒を進める方策
このような状況を突破し、初歩的なデータ活用の段階からモノづくりDXへと駒を進めるには、戦略策定と体制面の整備が必要です。このため、KMCは製造部門の課題や不具合の棚卸しからスタートします。そして棚卸しの結果に基づき、「不良品の率を半減する」「設備稼働率を20%改善する」など、やりたいことを明確化して現場と調整してQCD注目標を定量的に設定します。
注:生産管理の基本となるQuality(品質)、Cost(生産費)、Delivery(納期)の3つの要素の頭文字を取った造語。
しかし、DXは通常の「カイゼン」と異なり、特別な配慮が必要となります。その理由は、従来の「人」に頼ったアナログ的なカイゼンの仕組みを、「データ」を活用したデジタルカイゼンへと革新するものだからです。職人的な勘と経験が幅を利かす日本の製造現場では、意識や考え方から変える必要があります。困難性が高い取り組みなのです。
この困難を克服する基本はスモールスタートです。対象設備を定め、達成が容易なQCD目標から始めます。そして、データを活用するカイゼンについて、丁寧に説明し、現場の人が使えるようにします。ポイントは納得感です。現場では不具合が発生する原因が分からず、勘と経験で対応しているケースも多いので、データを示しながら例えば「金型に熱溜まりができており、高温になった金型の冷却が追いついていない。これが成形不良の発生原因となっている。これを防ぐには、温度管理をしっかりすれば良い。」など論理立てて説明すると納得感が得られ、現場がやる気になるそうです。
また、DXを進めるには、時間と手間がかかるので体制整備も必要です。KMCでは、次の3つの要件で人材を集めることを推奨しています。
① 改善項目単位に小グループを設置して、デジタルカイゼンを推進する(製造、生産技術、情報
システムのDXを推進する三位一体チームの設置等)
② 新しいものへの抵抗感が少ない人材を確保するため、可能な限り若い人材を集める。また、
教材としてセンサを揃えて提供する
③ 既成概念にとらわれない創造力を発揮してもらうために、さまざまな部門から人選し通常業務の
内容にとらわれない組織体とする(プロジェクト化等)
さまざまな部門から人を集めるのは、いろいろな知見が必要なこと、そしてプロジェクトの成果と考え方を全社展開するためです。新しいものへの抵抗感が少ない人材については、会社のやり方に完全には染まっておらず、かつ、実務は良く分かっている30代の若手が中心となるケースが多いようです。
また、プロジェクトチームにはそれを率いるキーマンがいて、全力でプロジェクトを引っ張ることが必要です。KMCはプロジェクト・リーダの役割として次の3点をあげています。
① メンバーのやりたいことを実現させる。
② 改善の成果をまとめ、期待した効果が出ていることを経営層へ正しく伝える
③ 常に3年先、5年先を見て、実施事項を決め、ぶれないで着実に進める
一方、経営者は成果が出るまでに時間を要することを理解し、DXに挑戦すると決めたら現場の状況を注視しつつ、不退転の決意で進める覚悟が必要です。また、DX導入に際し、投資対効果だけで判断しないことも重要です。具体的には小さなものであっても、成果が見えると現場はDXに向けて動き始めます。そのポイントとなる事項は、会社の中で「データを取る→見る→分析→活かす」というPDCAサイクルを回せるようにすることです(図2参照)。
図2:KMCが提唱するDXの進め方
「データを取る→見る→分析→活かす」というPDCAサイクル
(出所:KMC提供資料)
6. DX実現の早道は人材の再教育
業界からは、データ活用に不慣れな会社でもモノづくりDXが実現できるように、方法論を早く定式化してほしいと要望があるそうです。残念ながら現時点ではまだこれは実現していませんが、DXが進んでいる会社の現場管理職に話を聞き、試行錯誤で進める方法を佐藤社長は勧めています。DX人材育成は、現場発で進めないと定着しないからです。
この話を聴いて感じたのは、急がば回れで組織的なデジタル教育がDXの早道だということです。デジタル教育を受けている若い人達にとっては、DXは当たり前の変化です。問題はデジタルとは今まで縁がなかった人達です。経営者を含むこの人達を再教育することで、DXの意義や必要性を説明する手間やデータ活用の「いろは」を現場で教える必要性がなくなります。「データを取る→見る→分析→活かす」というPDCAサイクルを回すまでに必要な時間が、大幅に短縮すると考えられます。
DXに成功した強い中小企業数の増加は、我が国の製造業の活性化と競争力強化につながります。コロナ禍とロシアのウクライナ侵攻で、サプライチェーンの見直しが始まり、製造業の日本回帰の声を聴くようになりました。このタイミングをとらえてモノづくりDXが進展し我が国の製造業の復権につながること、それから「製造現場の改革なくして成長はない」と社長自ら強調されているKMCのさらなる発展を期待したいと思います。
【関連記事】
【ここに注目!IoT先進企業訪問記 】第5回モノづくりの仕組みを変える-KMCのユニークなコンサルティング
今回紹介した事例
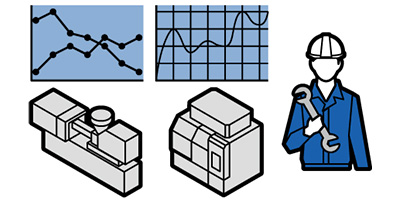
現場のデータを「取る・見る・分析・活かす」~製造現場の現状を打破するKMC のDXソリューション~
当社は「製造現場の改革無くして成長はない」という代表の持論のもと、製造現場のDX化を支援する企業としてに設立された。特に、ここ3年はセンサの開発に注力している。製造現場を見渡すと工場の設備の98%は古い設備であり、最新鋭のIoT対応の設備が入っているところは非常に少ない。古い設備をDX設備に転換するには、簡単に設置できる無線センサが必要なのである。…続きを読む
IoT導入事例の募集について